Lean of Six Sigma? Deel 2: Kenmerkende verschillen
Over waste gesproken
Er zijn veel verschillen te noemen tussen Lean en Six Sigma. Toch helpt het om er enkele uit te lichten. Van daaruit verkennen we de manier waarop de twee elkaar versterken of welke van de twee het best past in jouw organisatie. Ik ga bewust niet in op de tools, daar is al genoeg over geschreven (zie enkele links aan het einde van dit hoofdstuk), maar meer op de verschillen die ik zie in de cultuur, achtergrond en de dynamiek van Lean en Six Sigma.
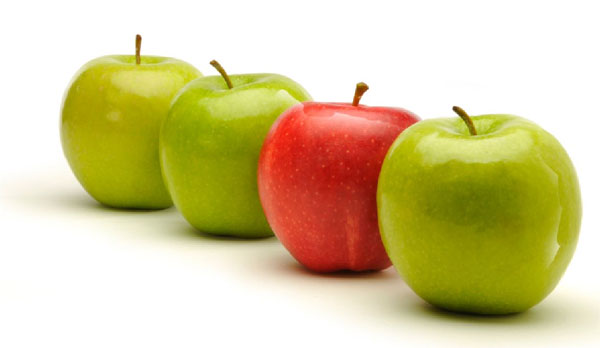
Verschil 1: Historie en culturele achtergrond
Beschrijving van de (verschillen) in culturele achtergrond van Lean en Six Sigma kan een boek vullen. Ik beperk me tot de opvallendste verschillen in de herkomst van Lean en Six Sigma.
Lean, zoals we het vandaag de dag kennen, is zoals bekend gebaseerd op het Toyota Productie Systeem. De wortels van het kwaliteitsdenken van Lean gaan echter terug tot de 19e eeuw, toen het toenmalige Toyoda nog weefgetouwen produceerde. Een kleine weeffout maakt een tapijt waardeloos, omdat herstel achteraf bijna niet mogelijk is. Zie daar de noodzaak om kwaliteit ‘in te bouwen’ in het proces.
Toyota Motor Company is in 1933 begonnen als divisie van Toyoda Automatic Loom Works, fabrikant van geautomatiseerde weefgetouwen. De basis van het kwaliteitsdenken van Lean, ‘Ingebouwde kwaliteit’ of Jidoka, is reeds in 1896 gelegd toen Sakichi Toyoda een tool bedacht waarmee het weefgetouw automatisch stopte als een weefdraad brak. Zo voorkwam hij de productie van ‘defecten’. Ook werd het hierdoor mogelijk meerdere weefgetouwen tegelijkertijd te bedienen. Mede beïnvloed door het boek ‘Self Help’ van Robert Blatchford, combineerde Sakichi Toyoda deze vondst met autonomie voor de medewerkers. Het ‘stop the line’ principe is hier het meest zichtbare deel van. Daarbij heeft elke medewerker het recht de productie stil te zetten als er een DMADV fout geconstateerd wordt, om vervolgens direct het probleem op te lossen en de root cause te onderzoeken. Dit wordt ook wel ‘autonomation’ genoemd: automatisering met behoud van autonomie voor de medewerker.
De meest ‘zichtbare’ oplossing voor het inbouwen van kwaliteit, automatisering, geeft geen prikkels voor continue verbetering. Sterker: automatisering focust vooral op productiviteit en kan bij verkeerde implementatie zelfs leiden tot afstomping van de medewerkers. Toyoda begreep heel goed dat hij voor continue verbetering de bevlogenheid van medewerkers moest aanspreken en dat hij ze daarom een grote mate van autonomie moest geven. Het ‘stop the line’ principe is hier het meest duidelijke voorbeeld van.
Fundamenteler dan de historie van Toyota, is wellicht de manier waarop het kwaliteitsdenken van Lean is ingebakken in de Japanse bedrijfscultuur. Typerend hierin zijn zaken als gezamenlijk belang & consensus, hiërarchie & structuur en ook het voorkomen van risico’s. De grondhouding om dingen goed over te dragen, vaak omschreven als ‘foutvrij van mij’, maakt dat medewerkers in hun denken en handelen ander gedrag laten zien dan hetgeen wij in onze cultuur gewoon zijn. En toch, als je de 5 managementprincipes van Sakichi Toyoda tot je neemt, zie je een universeel toepasbare set voor elke organisatie die verantwoord wil ondernemen:
Five Main Principles of Sakichi Toyoda
- Always be faithful to your duties, thereby contributing to the company and to the overall good.
- Always be studious and creative, striving to stay ahead of the times.
- Always be practical and avoid frivolousness.
- Always strive to build a homelike atmosphere at work that is warm and friendly.
- Always have respect for spiritual matters, and remember to be grateful at all times.
Deze 5 managementprincipes sluiten op het eerste gezicht aan bij onze calvinistische inslag. Hard werken, vooruitstrevend, niet te veel poespas. Maar tegelijkertijd: hoe ‘dankbaar’ ben jij eigenlijk? Hoe vaak verwijzen we naar ‘de organisatie’ of ‘ het management’ als dingen niet goed gaan? En zeggen we dus niet: ‘wat kan ík doen om de dingen beter te maken?’ In dit licht is het interessant om dit filmpje eens te bekijken, waarin de werkelijke betekenis van Kaizen wordt toegelicht. Stel jezelf eens de vraag: hoe bereid ben jíj om een offer te brengen in het algemeen belang?
Kortom: veel van de zichtbare elementen van Lean steunen op een manier van denken die ons niet in de genen zit. Als je hier geen aandacht voor hebt, zal je weinig succesvol zijn in de transformatie naar een Lean werkende organisatie.
Six Sigma is in de jaren ’80 ontstaan bij Motorola als kwantitatieve benadering om effectiviteit en efficiency van de organisatie te verhogen, maar vooral bekend geworden door General Electric. Het succes van de inzet van Six Sigma binnen GE is verbluffend, met bijna 1,5 miljard aan gerapporteerde besparingen in de eerste 3 jaar na introductie. Er zijn diverse interessante publicaties en boeken verschenen over het succes van Six Sigma. Op het web zijn inspirerende interviews met Jack Welch te vinden waarvan deze misschien wel de bekendste is. Jack Welch kan als geen ander uitleggen waarom ‘alles wat je in de organisatie doet, in dienst moet staan van het creëren van klantwaarde’.
GE is niet voor niets een van de meest succesvolle Amerikaanse bedrijven met duurzame financiële resultaten en een jaarlijks groeiende omzet en bedrijfsvoering. Van een bedrijf dat vliegtuigmotoren en kerncentrales ontwikkelt, mag je een diepgeworteld kwaliteitsdenken verwachten. De CEO laat er geen misverstand over bestaan hoe het staat met de wil om continu te verbeteren:
Toch zijn er belangrijke verschillen met de culturele achtergrond van Toyota en Lean. Meer dan de Japanse, gaat de Amerikaanse bedrijfscultuur uit van het succes van het individu, (beloning van) het nemen van risico’s, het verhogen van de DMADV Return on Investment en aandeelhouderswaarde. ‘The American Dream’ gaat inmiddels zo ver dat je als (internet)ondernemer pas meetelt als je een keer failliet bent gegaan.
Het voert te ver om deze beeldspraak op GE te projecteren, maar het is veelzeggend, dat Jack Welch Six Sigma in 1995 omarmde als ‘The Genetic Code of Our Future Leadership’. Moest er een verandering in de cultuur van het management van de organisatie doorgevoerd worden? Was de focus te veel verschoven naar ROI en (korte termijn) resultaten?
Hoe dan ook: het succes van Six Sigma is gevormd binnen de bedrijfscultuur van GE. Je ziet dit bijvoorbeeld terug in de implementatiestrategie van Six Sigma binnen GE, die een sterk ‘top down’ en gedreven karakter kent, met een keiharde focus op het behaalde resultaat.
Deze top down gedreven implementatie, was zeer succesvol bij GE en toch zijn veel organisaties in Nederland vastgelopen in het kopiëren van deze strategie. Waarom? Omdat deze niet aansluit bij onze (bedrijfs)cultuur, waarin wordt gestreefd naar consensus en draagvlak. Er is niks mis met de resultaatgerichtheid van GE, ook Toyota is een resultaatgerichte organisatie. Maar Lean en Six Sigma zijn ontstaan vanuit een sterk verschillende achtergrond en cultuur. Het is belangrijk deze verschillen te (her)kennen als het gaat om de toepasbaarheid ervan in jouw organisatie. En na te denken welke implementatiestrategie passend is voor jouw situatie.
Verschil 2: Probleemdenken versus oplossingdenken
Van een andere orde, maar wel opvallend, vind ik het verschil in dynamiek tussen Lean en Six Sigma. Door de opbouw van DMAIC ligt bij Six Sigma de nadruk vaak vooral op het probleem: ‘Wat is het Probleem (Define); Hoe groot is het Probleem (Measure) , Wat is de oorzaak van het Probleem (Analyse); Wat is de oplossing voor het Probleem (Improve).’ Het is om moe van te worden. Is dit waarom mensen Six Sigma vaak associëren met lange en moeizame trajecten? Ik chargeer, maar het doet toch wel wat met de energie die om zo’n verbeterproject hangt.
Lean werkt meer naar de oplossing toe: ‘Wat is de huidige situatie (Current State)? Wat is de doeltoestand (Future State)? Welke obstakels belemmeren je om die doeltoestand te bereiken? Welke gaan we aanpakken?’ Actiegericht, met een duidelijke visie hoe het proces eruit zou moeten zien.
Het ontbreken van een duidelijke visie is een valkuil waar veel Six Sigma-trajecten in belanden. Er worden verbeterprojecten gestart, zonder een duidelijk beeld van de doeltoestand waarnaartoe we willen bewegen. We zijn aan het verbeteren zonder richting.
LEAN kan hier een waardevolle aanvulling geven. Hoe ziet de ideale (gedroomde) situatie eruit? Werken met een ideale situatie in het achterhoofd helpt in mijn ervaring ook enorm om de échte oorzaken boven tafel te krijgen. Mensen zijn geneigd om vanuit het bestaande referentiekader te denken. Als je ze een gedroomd einddoel voorlegt, dan krijg je argumenten als ‘Ja maar dat kan dus nooit in 1 standaard werkwijze, want in de werkelijke situatie hebben we heel veel uitzonderingen’ of ‘Het klinkt wel leuk, beginnen en in 1x afmaken, maar in praktijk ontbreekt het vaak aan de juiste informatie en worden we regelmatig gestoord’. Het zijn prachtige aanknopingspunten om de ‘5X waarom’ vraag te stellen en op zoek te gaan naar de root causes.
Tip: stel in het begin van een DMAIC-project altijd eerst de vraag: zijn er al zaken die we direct kunnen aanpakken? En als die obstakels zijn weggenomen: is het nog steeds nodig om een DMAIC-aanpak te volgen, of is een aanpak met PDCA of Kata wellicht meer op zijn plaats om de overgebleven obstakels weg te nemen?
Dit lijkt vloeken in de ‘Six Sigma kerk’, maar je helpt zo voorkomen dat er DMAIC-verbeterinitiatieven starten die eigenlijk geen DMAIC-aanpak vragen. Door obstakels direct weg te ruimen creëer je energie en draagvlak. Je krijgt ook beter zicht op de werkelijke issues in het proces. Zo vergroot je de kans op een succesvol DMAIC-project.
Verschil 3: Continu versus projectmatig verbeteren
(…en valkuilen bij het verkeerd inzetten ervan.)
Het laatste verschil dat ik wil benoemen, is dat van Continu Verbeteren versus projectmatig verbeteren. Lean en Six Sigma streven hetzelfde doel na: een organisatie die zichzelf continu verbetert. Maar de weg er naartoe verschilt.
Six Sigma zet een verbeterstructuur neer met Belts ‘naast’ de lijnorganisatie, waarbij een continue stroom van verbeterprojecten wordt uitgevoerd. De aanpak van Six Sigma is die van DMAIC (projectmatig verbeteren). DMAIC-projecten hebben als doel om in een grote stap een doorbraak te forceren in de prestatie van een proces. In de Control fase wordt veel nadruk gelegd op de borging van het bereikte resultaat, immers een project is eindig.
Lean organiseert het verbeteren als onderdeel van het dagelijks werk, ‘binnen’ de lijnorganisatie. De doorbraak moet voortkomen uit veel kleine stapjes, middels PDCA (Continu Verbeteren). PDCA gaat er vanuit dat het verbeteren een continu proces is, zonder einde. Deze PDCA-cyclus wordt ingezet op alle niveau’s (operationeel, tactisch en strategisch). Onderstaand plaatje visualiseert dit verschil:
Continu verbeteren met richting Projectmatig verbeteren
PDCA en DMAIC kunnen elkaar hierin aanvullen. PDCA gaat verder waar DMAIC stopt. Sterker: vaak kom je er binnen je DMAIC-project achter, dat er in een proces niet geleerd wordt van gemaakte fouten. Anders gezegd: er is geen PDCA-cyclus ingericht!
Wat je vaak mis ziet gaan, zijn 4 zaken die elkaar (negatief) versterken:
- DMAIC inzetten waar PDCA meer op zijn plaats is. Zie ook de vorige paragraaf: als je zicht heb op de oorzaak/oplossing, moet je daarmee beginnen en geen DMAIC inzetten;
- Besluitvorming te ver van de werkvloer organiseren. De DMAIC-aanpak met behulp van tollgate-reviews geeft structuur aan het verbeterproject en dwingt betrokkenheid van het management af. Maar daarmee ontstaat ook het risico dat de besluitvorming rondom verbeteringen te traag en te ver van de werkvloer plaatsvindt. De bij Six Sigma vaak gekozen Top-Down-implementatie versterkt dit;
- DMAIC projecten ‘lukraak’ inzetten. Indien je projecten inzet ‘daar waar er brand woedt’ zal je op dat deel van het proces of binnen betreffende afdeling wel een effect bereiken. Maar aangezien de keten zo sterk is als de zwakste schakel, zal van veel losse initiatieven nauwelijks impact op de klant merkbaar zijn. Je bereikt pas impact als verbeterprojecten gestart worden vanuit een duidelijke visie en als de diverse DMAIC-projecten ieder bijdragen aan hetzelfde doel (binnen dezelfde ‘Waardeketen’). Policy Deployment kan helpen de aandacht te richten. Later meer hierover;
- Projecten zijn eindig, DMAIC niet. DMAIC is weliswaar projectmatig verbeteren, maar dat wil niet zeggen dat de verbeteringen ‘eindig’ zijn. Onderdeel van de Control fase van de DMAIC, is dan ook het inbedden van het continu verbeteren van het bereikte resultaat. Althans, zo zou het moeten zijn. Te vaak zie je dat dit niet of onvoldoende gebeurt en dat de implementatie van de oplossing aan ‘de lijn’ wordt overgelaten of dat er geen lerend vermogen wordt ontwikkeld. Het verwachte resultaat wordt dan niet bereikt of vervalt na verloop van tijd.
Maar ook geldt: in sommige situaties is een probleem dermate complex, is de urgentie te groot of zijn de problemen afdelings-overschrijdend, waardoor PDCA niet voldoende houvast geeft. In dergelijke situaties heeft de projectmatige benadering van DMAIC meerwaarde en kan de bijbehorende projectstructuur en tollgate besturing helpen het gemeenschappelijk belang te bewaken.
Meer info over verschillen tussen Lean en Six Sigma:
- Wat is Lean Six Sigma?
- Hoe is Lean Six Sigma opgebouwd?
- Wat is Lean?
- Is Six Sigma of Lean Six Sigma beter voor uw organisatie?
- Het selecteren van verbetermethodes
- De vergelijking tussen Lean en Six Sigma (Engels)
Over de Auteur
Paul van Sonsbeek was als Master Black Belt verbonden aan UPD. Hij heeft als trainer en coach een veelheid aan Lean en Six Sigma projecten en implementaties begeleid in diverse sectoren, met name binnen de financiële dienstverlening, overheid, logistiek en retail.